Advanced Crawler Mounted DTH Drilling Rig
Our company independently developed an advanced crawler mounted dth drilling rig that is safe, environmentally friendly, and efficient. This machine can be widely used in various open-pit mines, quarries, construction sites, and other occasions. The essence of DTH rock drilling is to make the impactor dive into the hole during rock drilling to reduce the energy loss caused by the impact energy transmitted by the drill rod, thereby reducing the effect of hole depth on rock drilling efficiency. Down-the-hole rock drilling equipment is a down-the-hole drilling rig. YQ-80, YQ-100, and QZ-165 are commonly used in China's underground mines.
I. Overview
The all in one dth automatic drill rig consists of a slewing mechanism, a lifting mechanism, a pushing mechanism, a support mechanism, and an impact mechanism.
Second, the lane column type
An automatic crawler mounted dth drill rig is an impact rotary drilling rig. Its internal structure is different from that of ordinary rock drills. Its gas distribution and piston reciprocating mechanism are independent, that is, the impactor. The front end is directly connected to the drill bit and the rear end is connected to the drill rod. When rock drilling, the impactor dives into the hole, and through the gas distribution device (valve), the piston (hammer) in the impactor reciprocates against the drill tail so that the drill bit impacts the rock at the bottom of the hole. The high-speed rotation of the impactor in the hole is achieved by a separate turning mechanism, that is, a motor or a wind-driven rotating device outside the hole, through a drill rod connected at the rear end of the impactor. Rock dust generated during rock drilling is flushed out of the hole by a mixture of wind and water. The mixed gas is injected into the impactor by the powder discharge mechanism through the center of the drill pipe, and then enters the bottom of the hole through the air groove on the impactor cylinder.
Third, drilling machinery
There are two types of rock drilling rigs and drilling rigs. There are open rigs and downhole rigs.
1. Rock drill
Used for drilling blast holes with a diameter of 20 to 100 mm and a depth of fewer than 20 meters in rocks above medium hardness. According to its power, it can be divided into pneumatic, internal combustion, hydraulic and electric rock drills. Among them, wind rock drills are the most widely used.
2. Open-air drilling rig
According to different working mechanisms of broken ore, it is divided into steel wire impact drill, down-the-hole drill, cone drill, and rotary drill. Due to its low efficiency, steel wire rope drill rigs have gradually been replaced by other rigs. Down-the-hole drilling rigs use a drill rod to drive the wind-driven impactor to rotate with the drill bit. The piston of the wind-driven impactor is used to impact the drill bit to break the ore. The roller cone rig is used to crush the ore rock by the rolling action of the roller bit. It is suitable for drilling holes with a diameter of 150 to 440 mm in hard ore rock. widely used. Down-the-hole (or cone) drilling rig consists of impactor (or drill), slewing mechanism, lifting mechanism, pressure device, walking mechanism, slag drainage system, drill frame, and drill rod. Rotary rigs are only suitable for drilling softer rocks and coal.
3.Underground drilling rig
When drilling downhole blast holes with a hole diameter less than 150 mm, in addition to rock drills, small diameter down-hole drills of 80 to 150 mm can also be used. When drilling blast holes with a diameter of less than 70 mm in coal or softer rock, power drills or air drills are usually used. Electric motors (or air motors) drive drill pipes to drill holes. The spiral groove is discharged.
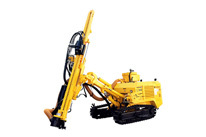
Advanced Crawler Mounted DTH Drilling Rig
评论
发表评论